SOURCE: ISRO
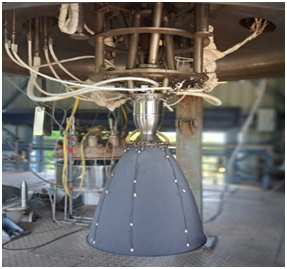
ISRO has achieved a breakthrough in rocket engine technology with the development of a lightweight Carbon-Carbon (C-C) nozzle for rocket engines. This innovationaccomplished by Vikram Sarabhai Space Centre (VSSC) promises to enhance the vital parameters of rocket engines, including thrust levels, specific impulse, and thrust-to-weight ratios, thereby boosting the payload capacity of launch vehicles.
VSSC, continuingits pioneering work in space research, has leveraged advanced materials like Carbon-Carbon (C-C) Composites to create a nozzle divergent that offers exceptional properties. By utilizing processes such as carbonization of green composites, Chemical Vapor Infiltration, and High-Temperature Treatment, it has produced a nozzle with low density, high specific strength, and excellent stiffness, capable of retaining mechanical properties even at elevated temperatures.
A key feature of the C-C nozzle is its special anti-oxidation coating of Silicon Carbide, which extends its operational limits in oxidizing environments. This innovation not only reduces thermally induced stresses but also enhances corrosion resistance, allowing for extended operational temperature limits in hostile environments.
The potential impact of this development is significant, particularly for the Indian Space Research Organisation (ISRO)’s workhorse launcher, the Polar Satellite Launch Vehicle (PSLV). The PS4, the fourth stage of the PSLV, currently employs twin engines with nozzles made from Columbium alloy. However, by replacing these metallic divergent nozzles with C-C counterparts, a mass reduction of approximately 67% can be achieved. This substitution is projected to increase the payload capability of the PSLV by 15 kg, a notable enhancement for space missions.
The successful testing of the C-C nozzle divergent marked a major milestone for ISRO. On March 19, 2024, a 60-second hot test was conducted at the High-Altitude Test (HAT) facility in ISRO Propulsion Complex (IPRC), Mahendragiri, confirming the system’s performance and hardware integrity. Subsequent tests, including a 200-second hot test on April 2, 2024, further validated the nozzle’s capabilities, with temperatures reaching 1216K, matching predictions.
The collaborative effort involved the Liquid Propulsion Systems Centre (LPSC) at Valiamala which designed and configured the testand IPRC, Mahendragiri which conducted the instrumentation and execution of the tests at their HAT facility.