SOURCE: RAUNAK KUNDE / NEWS BEAT / IDRW.ORG
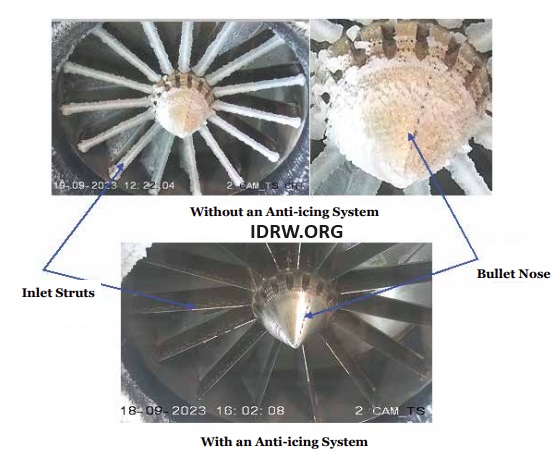

Icing remains a critical safety concern for aircraft, occurring when they fly through clouds containing supercooled liquid water droplets. These droplets freeze upon contact with aircraft surfaces, forming ice that can drastically alter the shape of airfoils, including wings and tails, leading to a deterioration in aerodynamic performance, difficulty in control, loss of flight stability, and, in severe cases, catastrophic crashes.
Ice dislodged from aircraft or engine surfaces poses additional risks, potentially damaging engines, causing loss of thrust, and leading to engine failures mid-flight. Historical data shows numerous fatal accidents attributed to aircraft icing.
To mitigate these dangers, aircraft and their engines require effective ice protection or anti-icing systems. Anti-icing systems prevent ice formation on aircraft and engine surfaces, ensuring safe operation in icy environments. Two primary types of anti-icing systems exist electrical and hot air-based systems. Electrical systems use electricity to heat the icing surfaces, while hot air-based systems utilize pressurized hot air from the engine compressor to heat the surfaces.
In India, anti-icing technology for aero engines was previously unavailable. Addressing this gap, the Gas Turbine Research Establishment (GTRE) in Bengaluru launched a technology development project aimed at designing and developing indigenous anti-icing technology for aero engines. Under this initiative, GTRE has successfully developed a methodology and capability to design a hot air anti-icing system for state-of-the-art gas turbine engines, applicable to both manned and unmanned platforms.
Ice typically accumulates on the engine inlet casing’s struts and bullet noses, as these components are exposed to ambient icing conditions. GTRE has designed heating configurations to prevent icing on these critical components. For the first time in India, two test pieces of the engine inlet casing have been produced using a combination of conventional and additive manufacturing techniques in a relatively short duration. To maximize the benefits of icing tunnel tests, four different anti-icing designs have been incorporated into a single test hardware.
The design methodology was validated using test data from icing wind tunnel tests conducted at M/s CIRA in Italy. The test hardware developed by GTRE demonstrated successful anti-icing capability under simulated icing cloud conditions, meeting all certification requirements.
With this achievement, GTRE now possesses the capability to design anti-icing systems for any advanced gas turbine aero engine. The expertise developed extends to conducting numerical studies to compute icing characteristics, such as water catch efficiency (catch coefficient), crucial for aero-engine or aircraft development programs. This technology holds promise for both military and civil aviation applications in the future.
NOTE : Article cannot be reproduced without written permission of idrw.org in any form even for YouTube Videos to avoid Copy right strikes. Websites doing illegal reproductions will get DMCA and Legal Notices.